Best for sliding parts
Lubricated hard anodizing with superior wear resistance
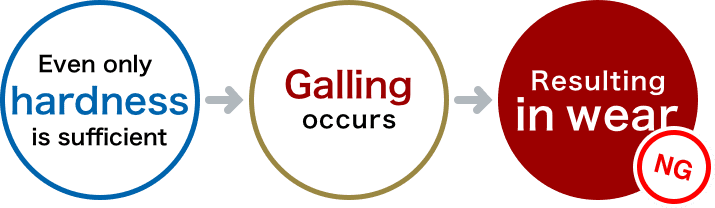
Would it be possible to solve this problem by adding a lubricating property to a hard anodized film?
This treatment was developed on the basis of this idea.
Kashima Coat®︎ is a lubricated anodizing intended to add the self-lubricating function to the hard anodized film to enhance wear resistance. The data obtained in wear resistance testing suggests that the lubricating property of Kashima Coat is approximately three to four times greater than hard chrome plating and four times than a hard anodized coating, respectively, which enables sliding parts to withstand friction with no lubrication.
Best for sliding parts
Anodized with superior wear resistance
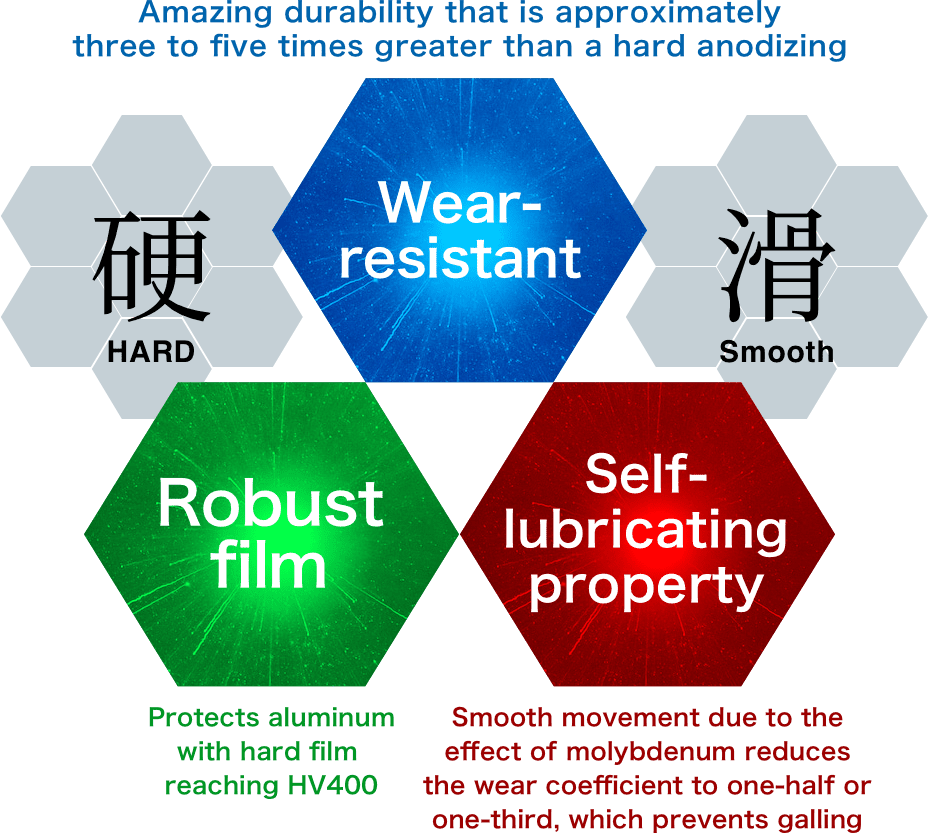
World's only technology
-
- Since the birth of the product
- Almost 40 years
-
- Recruitment results
- More than
500 - More than 5,000items
-
- Patented
- Domestic14
- Overseas1
-
- Trademark registration
- 38countries
Feature and Property
- Reciprocating sliding durability test
-
Test conditions
- Tester
- HEIDON FW14 surface property tester made by Shinto Scientific Co., Ltd.
- Speed
- 1,200mm/min
- Test piece
- ADC12 standard plate / Polish the surface with waterproof sandpaper in such a way that the height roughness becomes Rz 1.0 or lower
- Stroke
- 3mm
- Counterpart material
- A part made of SC45C (carburized and quenched) that is also used for products is mounted so that parts contact each other at an angle of 1 to 3 degrees
- Load
- 500g
POINTEven though the hardness
was the sameHard anodizing = The film was lost after reciprocating 100,000 times.
Kashima Coat®︎ = The film was retained even after reciprocating 400,000 times.
- Comparison of friction coefficient among surface treatments
-
Comparison of change in coefficient of friction for each treatment
POINTCompared with anodizing
The friction coefficient is approximately one-fourth
Reduces the initial friction coefficient / An effect of making an early transition to steady friction
- Structure of the lubricating anodized coating developed by Miyaki
-
The world's only technology
Superior lubricating performance is delivered, as long as the film is maintained, by precipitating molybdenum disulfide as a lubricating substance from the bottom of a countless number of pores created in the anodized film.
The number and size of pores
generated through anodizingIn an anodized film, a countless number of invisible pores exist.
The size of each pore is 10 to 30 nanometers (nm) in diameter.
It is said that there are several to 70 billion pores in one square centimeter, and such a dense number of pores can be compared to the earth’s population fitting easily into one square centimeter.“Hard” + “Smooth” = Resistant to wear
There are approximately several to 70 billions of combinations of hardness + lubrication in one square centimeter, which enhances the wear resistance more significantly than a hard anodizing.
Competitors' lubricating treatments
In the case of conventional lubricating treatments, the lubricating components have large particles that attach to the surface without entering the coating. Therefore, they disappear eventually, and lubricating performance is lost.
POINTKashima Coat does not lose lubricating performance but retains the low friction coefficient as long as the film exists.
- How Kashima Coat®︎ is formed
-
In a countless number of pores that are arranged regularly in the anodizing film generated through primary electrolysis, molybdenum disulfide accumulates as a lubricating substance from the bottom of the pores and eventually fills the pores to complete the Kashima Coat®︎.
- Observation photograph of the cross section of the film (EPMA photo)
-
POINT
As long as Mo remains within the range of the coating thickness,
post-processing of grinding, buffing, and lapping can be applied.
Table of properties according to aluminum types
Information on the compatibility with Kashima Coat, recommended coating thickness, coating hardness, and other factors is available.
Kashima Coat Black is a special type of Kashima Coat whose distinctive coloring changes to black while maintaining its lubricating property, wear resistance, and robust film as they are. This enables the adoption of Kashima Coat for products whose image color is unified to black. In addition, Kashima Coat Black can be utilized to prevent information leakage from products and can be introduced into sliding optical products because it can reduce irregular light reflection.
World's only technology
Features and Characteristics of Kashima Coat Black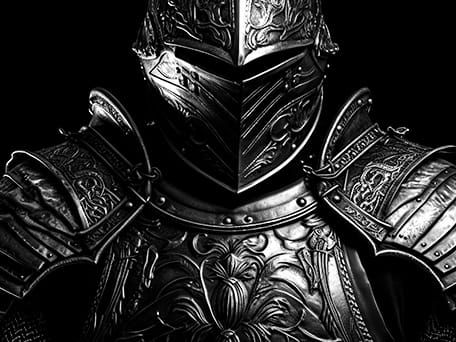
Genetic inheritance
While maintaining the lubricating property of conventional Kashima Coat,
Kashima Coat wearing coal-black armor expands the possibilities of products.
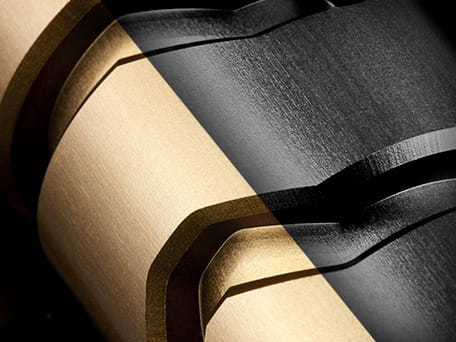
Taking advantage of features to make special
The distinctive color of Kashima Coat is blackened.
It enables the coordination of color matching that does not ruin the brand images of products.
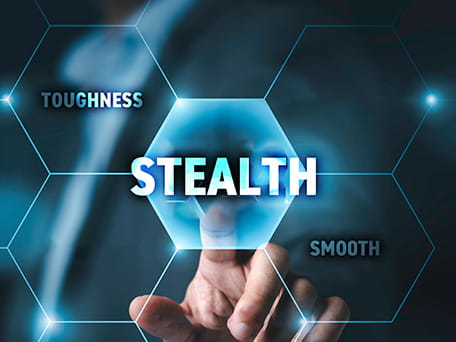
Realizing the concealment of information on adopted technology with stealth Because Kashima Coat has a distinctive color, the leakage of information on the use of Kashima Coat may be a concern because of its color. Kashima Coat Black has a color that is indistinguishable from a black anodizing, which enables elimination of such concerns.
Introduction examples
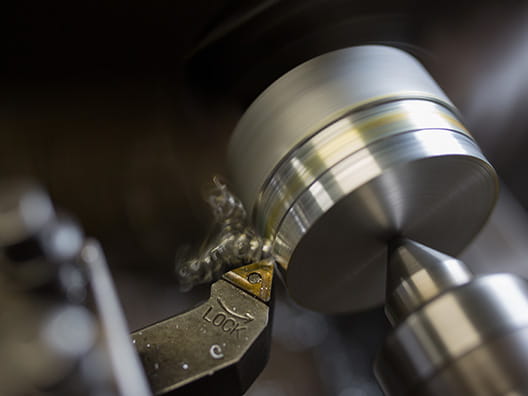
Components for equipment and machine tools
Sliding performance and special appearance
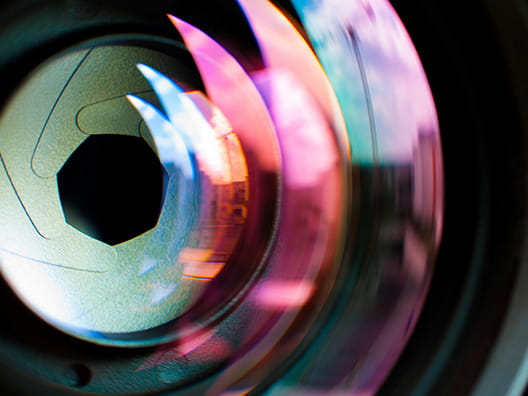
Optical components
Sliding function and prevention of irregular light reflection
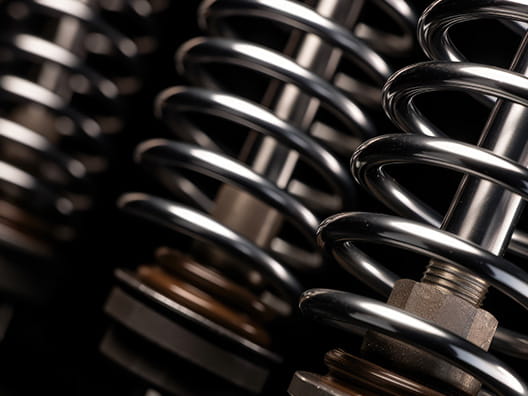
Suspension components
Sliding function and color coordination
Click here for inquiries about Kashima Coat Black