In the case of ordinary anodizing, the material surface becomes rougher after anodizing even if it is smoothed by machining and cutting. However, oxalic acid anodizing uses an entirely different treatment method, so the surface roughness of the formed film structure becomes similar to the one before treatment. In addition, the formed film is as thin as 3 to 5 μm, which causes fewer dimensional changes and is best for high-precision products.
While maintaining a fine surface roughness even after treatment,
making the aluminum skin more beautiful
OXALIC ACID ANODIZE
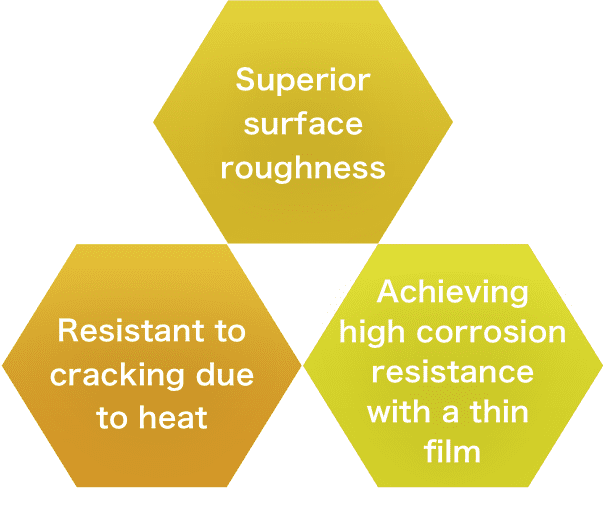
No polishing work is required after treatment
- Reduces manufacturing process
- Reduces manufacturing cost
- Achieves shortening of the manufacturing period
Achieves the effects of functional anodizing with a thin film
Adaptable to medical equipment and semiconductor devices
Few cracks are generated because thick cell walls are formed
Feature & Property
- Characteristics of superior surface roughness
-
Oxalic acid anodizing keeps almost equal surface roughness to that of materials before treatment compared with hard anodizing
POINTSurface roughness is approximately one-third of that of ordinary anodized coating = Creation of sealing surfaces and polishing work are not required
- High heat resistance
-
Cell structure of anodized coating
The cell walls generated through oxalic acid anodizing are thicker than the ones generated through the sulfuric acid method
Structural figure of sulfuric acid anodized coating
Structural figure of oxalic acid anodized coating
POINTMore resistant to cracking due to heat than ordinary anodized coating!
Change after heat treatment for one hour at 400˚C
Sulfuric acid anodized alumite oxalic anodized alumite Few cracks are generated in oxalic acid anodized coating with high durability even after heat treatment for one hour at temperatures as high as 400˚C
- High corrosion resistance
-
Oxalic acid anodizing is characterized by fewer generation of cracks than sulfuric acid anodized coating because thick cell walls are formed.
Therefore, it is less likely to cause delamination due to cracks and enhances corrosion and wear resistance.16 hours of CASS (Copper-accelerated Acetic-acid Salt Spray) testing
Oxalic acid anodizing film has superior corrosion resistance. Specifically, 3 μm thick oxalic acid anodizing film has higher corrosion resistance than 10 µm thick ordinary anodizing.
POINTHigh corrosion resistance can be achieved as corrosion (erosion) is less likely to occur because of thermal cracking.
Oxalic anodized alumite 3μm Alumite 10μm
Advantage of adopting oxalic acid anodizing
Elimination of the need for polishing leads to
Process reductionCost reduction Short time to delivery
- In the case of sulfuric acid (ordinary) anodizing
-
Hard anodized coating with a thickness of approximately 50 μm needs to be formed, and polishing is required after anodizing to maintain surface roughness
- In the case of oxalic acid anodizing
-
Adopting oxalic acid anodizing enabled the maintenance of surface roughness even after treatment
Comparison between sulfuric acid and oxalic acid
Sulfuric acid (normal) anodized aluminum | Oxalic anodized alumite | |
---|---|---|
Electrolytic solution | Sulfuric acid | Oxalic acid |
Hardness | Hv250〜350 | Hv200〜500 |
Surface roughness | △ | ◎ |
Occurrence of cracking | Occurs | Does not occur |
Corrosion resistance | ◯ | ◎ |
Dyeing Color | Acceptable | Not allowed |
Self-Coloring | Grey- or yellow-based color, depending on materials | Gold-based color |